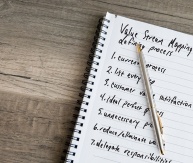
A useful tool for any CNC machine shop that wants to reduce costs and improve overall performance is Value Stream Mapping. Typically used as a starting point for Lean Manufacturing, Value Stream Mapping identifies and analyzes all of the activities involved in delivering a product to your customer.
The goal is to critically address every step in the manufacturing process, identify wasted labor, time or materials and reduce or eliminate their impact on the process. You can implement Value Steam Mapping by following these 7 steps:
- Document the current process. Be certain not to skip anything or take an activity for granted. You need to look upstream and downstream as well as at the machining cycle, itself.
- Identify and list every step in the process. What is the first step? Is it when you get the order from the customer? When you receive the part print? What is the last step? When shipped from your dock? When the customer receives it? Start with the earliest possible stage of the process and end with the point at which you’ve met or exceeded the customer’s expectations.
- Identify customer value. Once you’ve listed every step in the process, look at each step critically to determine which steps add value to the customer and which do not. What would happen to your costs and customer satisfaction if you could eliminate any steps that don’t add any value?
- Define what the perfect process looks like. If you could eliminate every bit of waste and deliver a product that has 100% value, what would that process look like? In this step, don’t encumber your thinking with practical concerns. It’s not likely you will ever be able to achieve the perfect process, but you need to visualize what it would look like if you could.
- Identify those parts of the current process that get in the way of perfection. Given the reality of your situation, how close can you come to the perfect state you envision in step 4? How many of the steps that add no value to the customer can you improve? For example, if you receive part prints in hard copy form, can you get a CAD file to simplify part programming?
- Identify major initiatives to reduce or eliminate waste. In step 5 you’ll identify areas that can be improved and develop possible ways to do so. Perhaps you need to upgrade to a machine tool that has greater capabilities. Maybe you simply need advice on tooling or fixtures. It could also be that your machine operators need additional training. If machine reliability is a problem, you may need a more effective preventative maintenance program.
- Assign tasks and responsibilities. Once you’ve determined what needs to be done, develop a plan for identifying viable resources, considering your options, making final decisions and implementing the plan steps. This plan should have clearly defined assignments for those involved and due dates for the various phases.
You may never achieve 100% through this process, but think of what an 80% improvement could mean for your business. Your Torrance Haas Factory Outlet will do its part by helping you get the most value from your CNC machines and accessories. Call: (310) 381-0750, email: jphillips@haasfactoryoutlet.com, or visit www.haasfactoryoutlet.com.