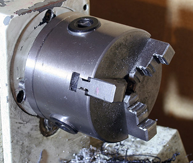
You can argue about who the hardest working person is in your shop, but no one disagrees that the standard 3-jaw chuck works as hard as any CNC machine component. It’s the primary workholding device that helps maintain accuracy and spindle speed.
Although it seems like a simple mechanism it actually contains a number of moving parts that require adequate lubrication at all times. A piston within a hydraulic actuator connected to the chuck by a drawtube typically enables the chuck jaws to open and close. The back-and-forth motion of the piston drives a plunger inside the chuck body to open and close the jaws, so it grips the work piece with appropriate force.
If these moving parts aren’t properly lubricated, the resulting friction will create wear points on the chuck. This can result in out-of-tolerance parts, scrap and rework. Not to mention the cost to replace a badly worn or damaged chuck. Fortunately there are some simple steps you can take to see that this doesn’t happen to yours.
- There are several grease fittings on the chuck housing, each of which should be regularly lubricated. How often the chuck needs greasing depends on the volume and nature of the work you’re performing. A good practice is to require machine operators or maintenance personnel to grease these fitting at the end of each shift or workday. That way you won’t run the risk of missing a lubrication cycle.
- Be sure to only use the type of grease specified in the operator’s manual for the CNC machine or chuck. Today most chucks require molybdenum grease because it holds up better under high temperature and pressure applications. A common mistake is to use whatever lubricant is handy. The viscosity and other performance differences among various lubricants are significant, and using the wrong one can damage the chuck components.
- Another contributing factor to premature chuck failure is setting the grip pressure to a level greater than what is needed to effectively hold the work piece. These additional gripping forces put a strain on the chuck systems and eventually cause the jaws to rock back and forth instead of maintaining constant pressure on the part. Along with poor lubrication, this can cause undue wear. CNC machine operators should determine optimum chuck pressure when setting up a parts run.
Performing these simple actions will keep your chucks operating reliably throughout their lives, saving you considerable time and money. Your Torrance Haas Factory Outlet has more productivity and cost-saving ideas for your CNC shop. Give them a call: (310) 381-0750, email: jphillips@haasfactoryoutlet.com, or visit www.haasfactoryoutlet.com.