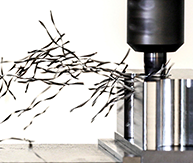
Because of the differences in their basic structures, composites react differently than metals during machining. Whereas we cut most metals by shearing away parts of an essentially uniform structure, machining composites involves cutting through the layers of its various materials. Each of these layers reacts differently to the action of the cutting tool.
For example, resins often used in the matrix layers tend to break off at the edge, while the reinforcing carbon fibers may be cut or merely fractured. Additionally, the heat generated by the machining process can cause composites to delaminate, thus ruining what is often a very costly part. Moreover, just as machining high-temperature alloys requires different tooling, cutting speeds and feed rates than more common metals, each type of composite material requires special consideration before machining.
Tool wear is a major concern because composite materials require extra-sharp cutting edges and consistent tool geometry suited to the specific components of the composite material. According to tooling producer Sandvik Coromant:
“In general, sharp cutting edges and sufficient clearance become more important when working with composites, in order to minimize the tool rubbing against the material. Tool wear can be especially problematic, as geometrical changes to the cutting edge often lead to excessive heat generation, edge breakdown, and problems with component quality.
When machining flat surfaces, operators must deal with demands that call for innovative indexable insert tooling. Facemills and endmills equipped with diamond-tipped or diamond-coated inserts often prove most effective with composites featuring high fiber content. For edging and trimming, a variety of solid carbide cutters, and carbide and diamond inserts, offer alternatives for achieving high levels of quality. In general, the cutting tools need to be easy-cutting, generating minimal cutting forces.
Diamond-tipped (PCD) drills and milling cutters tend to maximize tool life, as diamond stands up relatively well to the wear of various carbon fiber materials and stacked materials, including those that contain titanium. Diamond-coated solid carbide tools can provide a suitable alternative for edging, though typically at the cost of shorter tool life.
Drilling is the most common machining operation when working with composites. It presents a unique challenge, as material at the entry and exit points can splinter and even split into separate layers, which is known as delamination. Achieving suitable surface quality often necessitates extra effort in obtaining satisfactory cutting action between fiber layers and the matrix. Cutting speeds of 100mpm to 200mpm are common, typically paired with feed rates of 0.02mm/rev to 0.06mm/rev. Most composite drilling applications feature holes ranging from 3.0mm to 12.7mm.
For drilling fiber-rich CFRP materials, operators should look to geometries that reduce splintering. Drills using vein design, or sintered PCD cutting edges, can use a double-facet geometry to minimize the chances of delamination upon entry and exit. Resin-rich CFRP materials often demand a steeper helix angle to reduce the risks of delamination and splintering. For these types of composites, one should start with a spindle speed of approximately 2,000rpm for a small or medium tool, with a low feed rate. This allows the observation of machining properties that is necessary to correctly adjust cutting data and evaluate the effectiveness of a specific tool geometry or grade.”
Your Torrance Haas Factory Outlet and Sandvik Coromant work together to help CNC shops reduce tool wear while improving productivity. Learn more by calling (310) 381-0750, email: jphillips@haasfactoryoutlet.com, or visit www.haasfactoryoutlet.com.